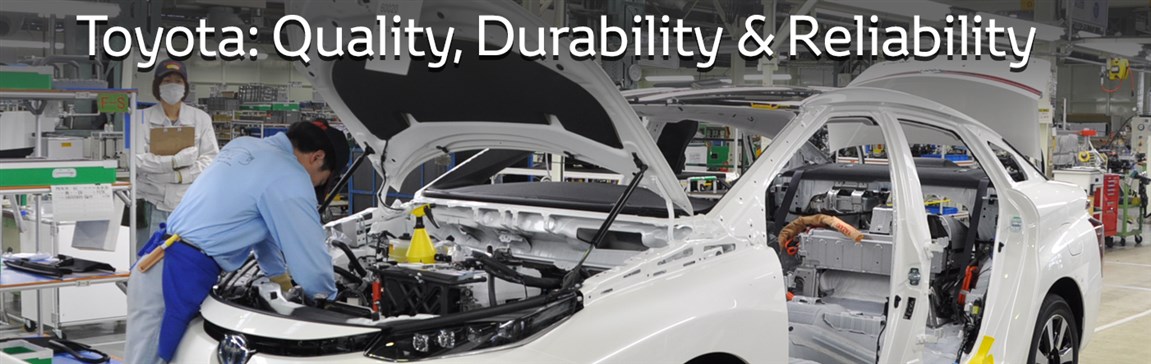
Dynamic Growth Based on Making Ever-Better Cars
Building ever-better cars is the introduction of TNGA, which revolutionizes the vehicle development framework.
The Toyota Global Vision announced in March 2011 describes our values and the kind of company we aspire to be. One facet of Toyota's efforts to build ever-better cars is the introduction of TNGA (Toyota New Global Architecture), which revolutionizes the vehicle development framework through the blending of planning and design. Toyota intends to raise the competitiveness of basic parts relating to ride, turning, and braking to world-class levels, and it is now able to standardize parts and units across different models through grouped development that puts multiple models through the planning process at the same time. For example, we have separately standardized the parts and units for compact, mid-sized, and large platforms (chassis) respectively. Based on the new vehicle architecture, we aim for full optimization by standardizing even more basic parts, including platforms and powertrains, across vehicle segments.
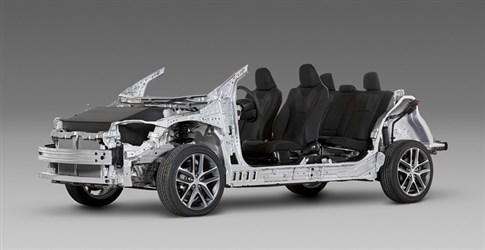
TNGA is our framework for making ever-better cars for a wide variety of customers and regions in smarter and more efficient ways, with the ultimate aim of creating products that stir our customers’ emotions.
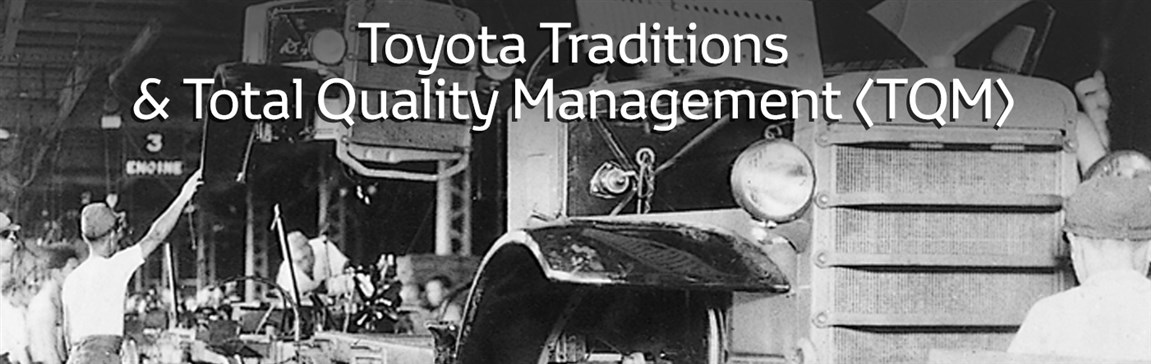
Since its foundation, Toyota has steadfastly carried out quality assurance activities resulting in top recognition and customer loyalty. Toyota is proud of its traditions stemming from the late founder’s father, Sakichi Toyoda and his automatic power loom.
Regardless of the year, Toyota remains true to the principles set forth by its founders and leaders. Many processes and philosophies that began during Toyota Motor Corporation’s foundation or earlier are still true today. For example, when Sakichi Toyoda was building his loom, he wrote: "You can't be creative and complete a piece of work unless, above all, you work on the construction yourself, attend carefully to every single detail, and experiment over and over again. And you must never leave the production to anyone else. These are the lessons I learned from experience, and they should be minded.”
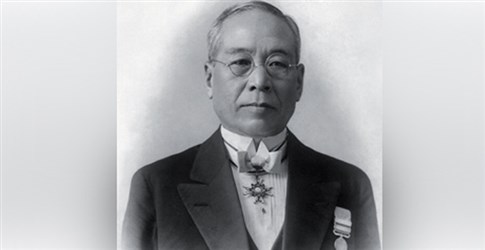
His lesson later gave way to Toyota’s Total Quality Control (TQC) activities designed to solve quality issues and ensure that they don't reoccur. Kaizen or continuous improvement was not only done by the founders but employees from an early stage were encouraged to provide their input. In 1951, Toyota launched the creative idea, “Suggestion System” to support and encourage employees in making effective contributions to the company’s production and development. This was soon rewarded in 1970 when Toyota Motor Corporation was the first company to receive the Japan Quality Medal for quality control management.
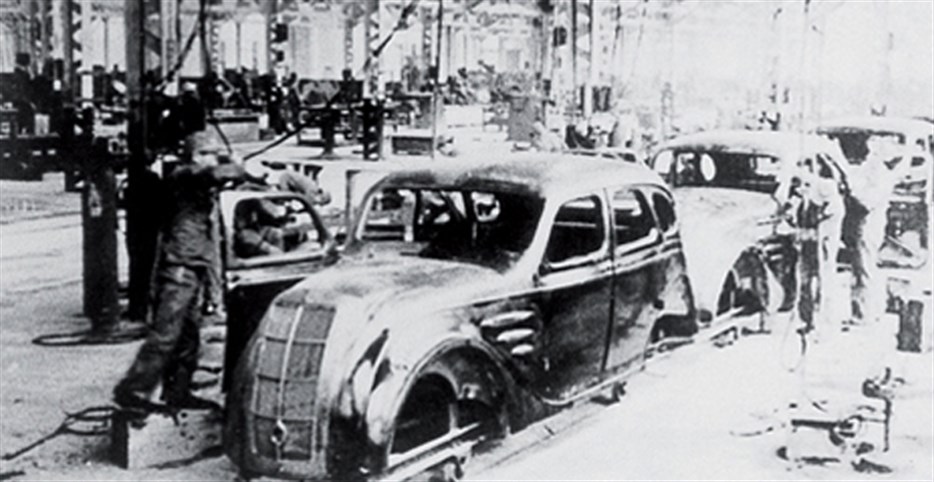
Customers remain at the heart of all quality processes. From the very beginning customers interests and safety were at the core of Toyota’s TQM. For example, when Japan issued a vehicle recall system in 1969 – Toyota learned from the recall issue by gathering accurate market information, check defects at each production process, improve production process control and carry out stricter inspections in order to eliminate the manufacture of defective products.
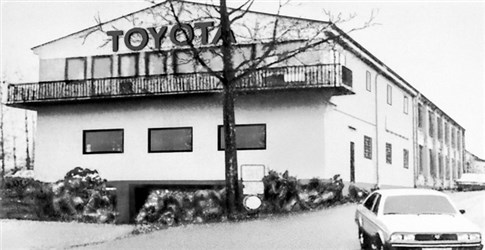
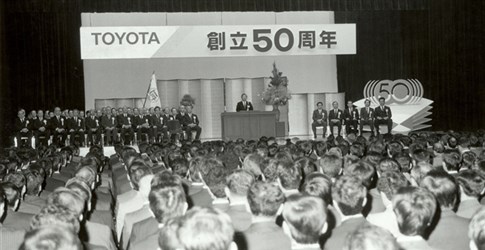
Due to its history and the roots of the Toyota Production System, the quality and reliability of Toyota vehicles improved greatly into the reputation Toyota carries today.
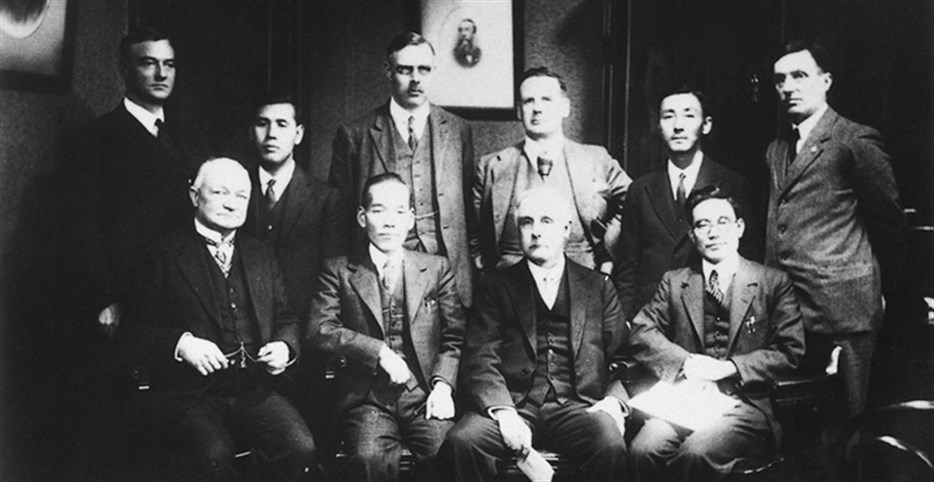
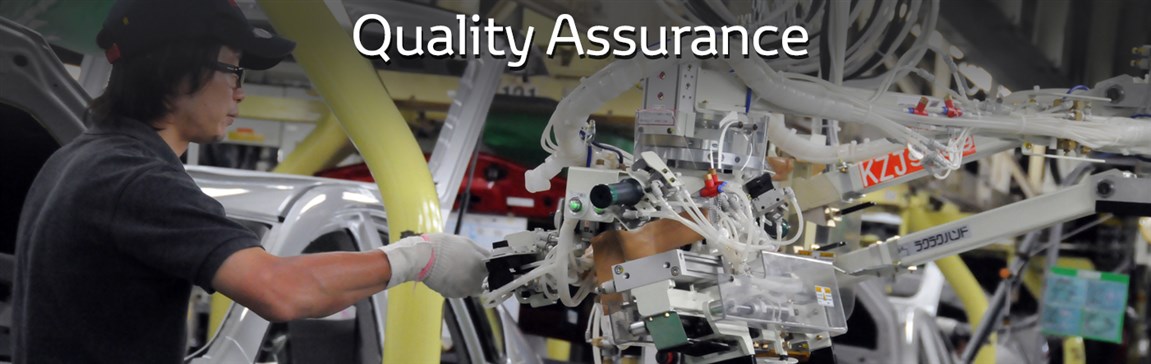
Toyota takes pride in the quality of both its products and its Toyota Way processes as well as the ability to improve (kaizen) and solve problems effectively from reoccurring has been necessary to ensure top quality.
“When customers purchase a Toyota, they are not simply purchasing a vehicle, truck or van. They are placing their trust in our company.” - Mr. Akio Toyoda (President, Toyota Motor Corporation)
This trust is taken seriously and have been adapted to the core principles behind Toyota’s quality assurance include: “Customer First” , “Quality First” and “Genchi Gebutsu” translated by “go and see at the scene.” Toyota experts are trained to rigorously check for quality through the production line and are empower to halt the production line for any fault. However, when Toyota vehicles reach the end of the production line, it’s only the beginning of an arduous set of quality assurance checks where experts screen each Toyota vehicle carefully. Over 2,000 checks are done on every Toyota vehicle before it leaves the factory and testing is completed on the bodywork, exterior trim, interior trim, engine testing, underbody, steering alignment, headlamps, special leak tests, anti-lock braking system, the electronic control unit and much more. The Toyota vehicle is even put under a special spot light to ensure no dents or scratches are present and the paintwork is done flawlessly. Going above and beyond – Toyota researchers and developers perform the following tests to ensure that every Toyota can be driven across the four corners of the world:
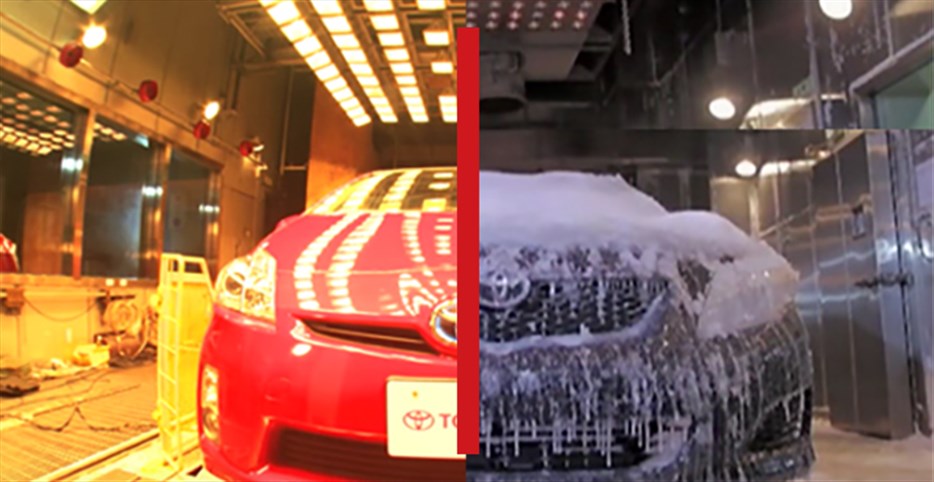
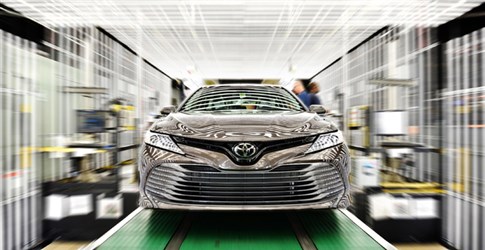
Toyota Cars are Tested in Harsh Conditions in Extreme Heat and Cold
Across the earth there are harsh environments that exceed the imagination. At Toyota's engine testing site, tests are conducted in facilities that can recreate the extreme cold and searing heat of different regions of the world to ensure that engines perform properly in any environment. These all represent Toyota Production System value, “poka-yoke” which translates to “mistake proofing". Faults are spotted and fixed before the Toyota vehicle reaches the customer. Toyota’s pride in its product is mirrored in its factory warranties given to every vehicle.
Vast Test Site
Collision tests are essential for protecting divers from danger and making safer cars. Collision tests using actual vehicles are conducted at a vast collision test site with a length of 280 m, maximum width of 190 m, and a surface area of approximately 44,000 square meters. Toyota performs more than 1,600 tests using actual vehicles (all are brand new cars) each year (including tests at other collision test sites). This means that on average, more than four tests are conducted each day. The vehicles used in the tests are destroyed, but by performing the tests over and over again, Toyota is able to extract valuable information under various conditions.
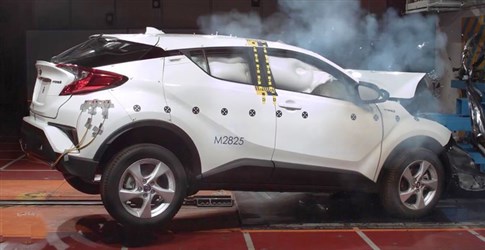
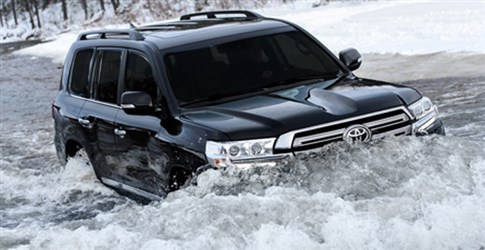
For Every Road in the World
Automobiles are not always driven on well-paved roads. Toyota conducts testing by recreating poor road conditions akin to those that exist around the world including flagstones, gravel roads, inclined roads, flooded roads, snow-covered roads, icy roads, and deserts. The testing for poor road conditions includes driving a total of 900 km in a single day including on actual roads with three drivers taking turns at the wheel. The testing of tires and other strengths are performed under the harshest, most adverse driving conditions.